If you have a manufacturing service, as well as you could enhance your manufacturing such that your item would certainly be made in about one and a half hrs as opposed to twelve hrs, would you accept the modern technology that could help you understand that possibility? That’s just what Henry Ford did simply over 100 years back when he innovated making use of the production line method to manufacture cost effective cars.
Henry Ford’s suggestion was to make automobiles that would certainly be budget-friendly to everyone in America, including workers in his very own factories. In order to do that, he had to make the production process far more reliable. Ford had actually been checking out the scientific administration theories of Frederick Winslow Taylor, who was an expert in time-and-motion research. Essentially, Taylor would certainly evaluate the time that was invested doing the different movements that were called for by a task or by different job sequences, so he might come up with a method to systematize work and also make workers and devices more efficient. Using Taylor’s theories, Ford had the ability to develop his own assembly line approach of making automobiles, hence making cars extra inexpensive to the masses.
From Fixed to Streamlined
When Ford first began production, employees would construct a vehicle in one area. Teams of employees would certainly bring the required components to the frame of the cars and truck and also construct the automobile, which was in a stationary placement. It took these groups about twelve hours to construct one car. The length of time it took to create one automobile and also the amount of cash it took to create it made it impossible for Ford to understand his desire for one auto for every single garage.
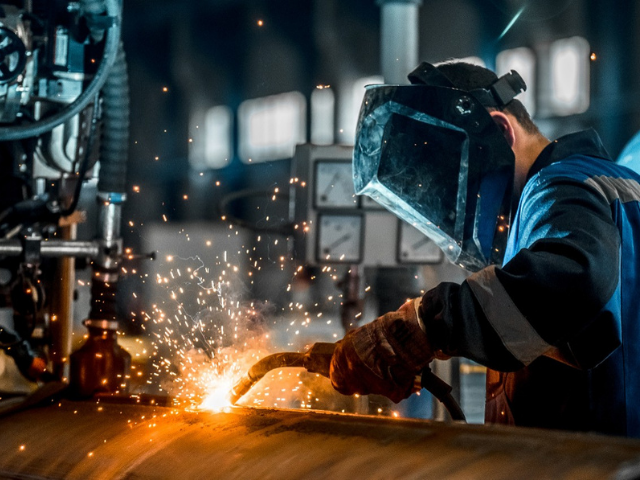
Ford wanted to figure out a means to improve the manufacturing procedure, so he resorted to Frederick Taylor to assist him boost his vehicle making approaches. Taylor recommended that Ford’s workers would certainly be much more productive if their jobs matched their skills and if they could avoid unneeded activities. When Ford initially hired Taylor, he most likely did not understand what an enormous adjustment he would certainly see in his auto manufacturing procedure. Find out more info on the metal spinning factory at this link.
Using Taylor’s concepts, Ford decided that the major parts of the vehicle, like the framework, need to remain in a set setting, and the smaller sized parts can then be transported to the auto when essential. Nonetheless, this was not nearly enough to streamline the process to Ford’s fulfillment, so he chose to maintain his workers stationary and have the cars and truck pulled through the assembly line of workers that would include the necessary automobile parts when the cars and truck body came through their work stations. This system was extra effective, however it wasn’t until Ford began making use of a power-driven system to take the vehicle framework with the assembly line that typical production time reduced to about a hr and a fifty percent. He got the idea after seeing meat packers take apart a cow carcass making use of a trolley system. He simply reverse-engineered it for the manufacturing of his cars.
In addition, Ford streamlined the system by using compatible parts as well as ensuring his robust, no-frills Version T was simple to drive and also maintain. He, really, did not also supply a choice of shades on the Version T. He informed people that they might have any kind of color Design T they wanted as long as it was black.